wood pellet manufacturing equipment
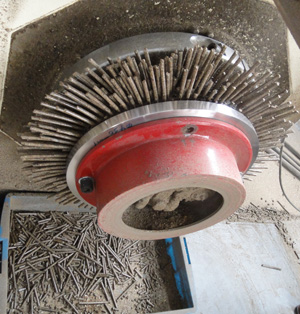
Wood pellet manufacturing equipments are the key factor for making wood pellets.
The entire process of producing wood pellets isn't as simple as may seem. The core process is compression of the wood into pellet form, though the raw material requires certain characteristics and features for the wood in order to be compressed into pellet form.
Wood pellet manufacturing equipments and animal feed pellet mill
The wood pellet manufacturing equipment its self also needs specific abilities that not all pellet manufacturing equipment has. The reason behind this is the majority of wood pellet manufacturing equipment was produced to process grass as well as other low density materials into animal feed pellets.
However there's still a large quantity of animal feed equipment promoted for that use of wood pellet manufacturing equipment. The simple fact is without changes to the raw material or equipment it's just not possible to make durable and quality wood pellet fuels. To begin with, producing wood pellets puts a lot more load on wood pellet manufacturing equipment, therefore many pellet mills made to produce animal feed pellets cannot cope.
Other general differences from a wood pellet manufacturing equipment and an animal feed pellet mill is rotation speed and compression temperatures. Animal feed pellet mills rotate at higher speeds, and are geared as such to obtain the highest productivity figures possible.
A animal feed pellet mill can rotate at higher speeds since the raw material is easier to compress, and generates less friction through the die. A wood pellet manufacturing equipment on the other hand has to rotate slower, for two reasons. The first reason is due to the increased density of the wood fibre, it takes more force to push the wood through the die. Placing wood into a animal feed pellet mill won't produce quality pellets, and more than likely stop as there is not enough power due to the gearing.
The second reason for the lower rotation speed would be to melt the natural lignin within the wood to bind the pellet together, the wood needs to stay in the hot die for an extended period. If the wood is pushed through the die too quickly, the lignin won't melt and also the wood will simply leave the pellet mill as dust not in pellet form. To assist to increase the flow of the wood through the pellet mill and get the wood up to the required temperature, a steam conditioner is often used in large scale production before the pellet mill. This reduces the resistance of the wood as it passes through the pellet mill while still having this required pellet compression. Steam conditioning is extremely energy intensive, however the reduced load on the pellet justifies the energy input. In small-scale production, steam processing is not practical because of the expense and the danger of high temperature steam. If pellet quality is an issue the wood fibre can be combined with binders and lubricants such a modified corn starch.
Wood Pellet Production Conclusions
From the above information, it should be clear that there are several variables that are not commonly considered in pellet manufacturing equipment. Another essential point may be the characteristics of each one wood species and biomass feed stock behave slightly differently. For instance a sample of sawdust with and without bark will work differently in the wood pellet manufacturing equipment. The reason is the lignin within the bark melts at a lower temperature in the pellet mill and helps to bind the pellet together. However most wood fuel pellets do not contain bark, as the bark will increase the ash content of the pellets, and many pellet stoves and boilers are not designed to be able to burn higher ash content wood fuel pellets.

